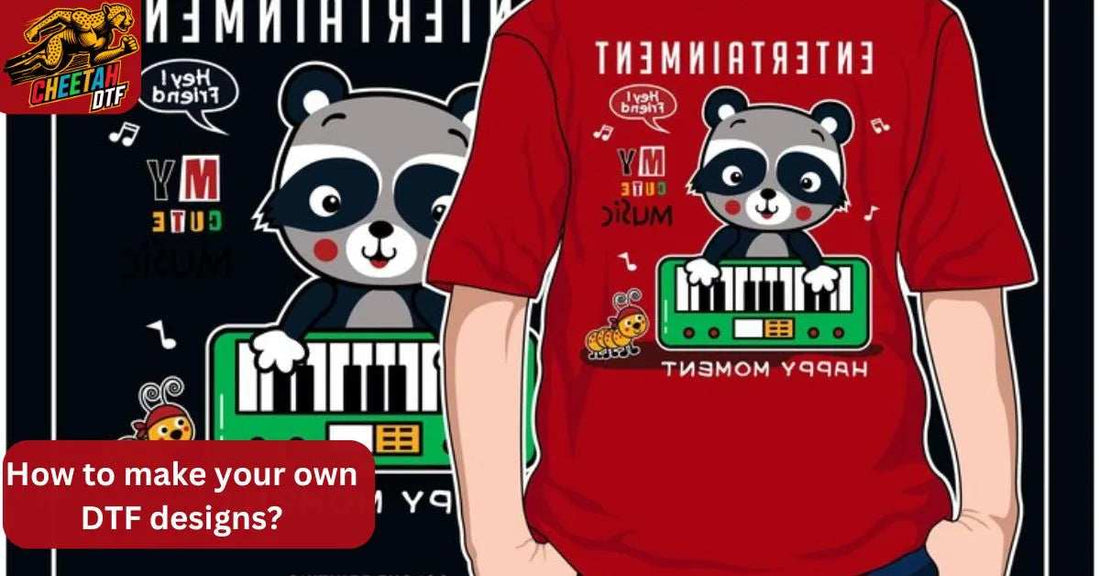
How to make your own DTF designs
Share
Bring the DTF Designs into your life today and discover untold worlds of creativity with Direct-to-Film (DTF) printing, which has permanently disrupted the custom printing industry. Its diversity, simple operation, and delivery of high-caliber prints on many diverse fabrics make it instantly popular with hobbyists and practitioners. This ultimate guide on creating your own DTF designs-from an idea to print-ready files-is excellent for beginners up to professionals. It showcases Cheetah DTF as the leading service provider in this area.
Essential Equipment for DTF Design Creation
To create DTF designs, you need specific equipment to ensure quality results. Thus, there is a worthwhile DTF printer that would print your design on a unique transfer film, and there's DTF ink that includes white and colors of vibrant prints. You need DTF film, a transparent medium that holds the design, adhesive powder holding the ink to the fabric, and a heat press. A lot goes on with these machines. Finally, add design software like Adobe Photoshop or CorelDRAW to create and touch up your artwork.
Step-by-Step Guide to Creating Your DTF Designs
Step 1: Ideation and Design Creation
Start with a clear idea of your design. Sketch it out on paper or directly in design software. Consider your target audience and fabric type.
- Choose the Right Software
- Resolution Matters
- Color Profiles
- File Format
Choose the Right Software
To create high-quality DTF designs, it's essential to use professional design tools like Adobe Illustrator, CorelDRAW, or Canva. These programs offer advanced features and precision for crafting detailed, vibrant artwork. Whether you're creating intricate logos, typography, or full-color graphics, these tools help ensure your designs are print-ready and of the highest standard.
Resolution Matters
Even so, it guarantees that your design work has a resolution of at least 300 DPI dots per inch. Such higher resolution is considered a prerequisite to sharpness and clarity during printing, as even tiny details rendered crisply and accurately will avoid pixelation or blurriness in the final output. A 300 DPI resolution is the industry standard for print designs, especially where digital-to-film transfer printing is involved.
Color Profiles
It is essential to set the RGB or CMYK color settings depending on your printer specifications, which ensures all colors are printed correctly. RGB is best for designs only displayed on the screen, while CMYK is frequently used in print media to provide the exact colors translated when they move to print.
File Format
In keeping with that need, you must use the right color space—either RGB or CMYK—per your printer's needs to get the most genuine print output. RGB is ideally meant for live works and screen displays, whilst CMYK would be your mainstay standard for print; thus, it is much closer to the output. The right color choice avoids color misalignment and ensures that the design will look exactly as it was meant to on the fabric.
Step 2: Prepare Your DTF Film
- Load the DTF film into the printer. Ensure the printable side is facing correctly.
- Check printer settings for optimal output.
Step 3: Print Your Design
- Print your design in reverse (mirrored) to ensure proper orientation during transfer.
- Apply white ink as a base layer to make the colors pop on dark fabrics.
Step 4: Apply Adhesive Powder
- Evenly coat the printed design with powder adhesive while the ink is still wet.
- Shake off excess powder to avoid clumping.
Step 5: Cure the Powder
- Heat the DTF film at around 160°C (320°F) for 2-3 minutes to cure the powder.
- Use a curing oven or heat press for consistent results.
Read Also How to Cure DTF Powder with Heat Press?
Step 6: Transfer the Design to Fabric
- Place the cured film on the fabric.
- Use a heat press machine at 160°C-170°C for 10-15 seconds.
- Let the film cool before peeling it off for a clean transfer.
Design Tips for Beginners
Beginners should start with simple, bold designs to ensure clarity and ease of transfer during printing. Focus on high-resolution artwork and experiment with colors to create eye-catching results while building confidence.
- Keep it Simple
- Use Bold Fonts
- Experiment with Colors
- Mockup Your Designs
Keep it Simple
Too elaborate designs are complicated to print and may not transfer well. Go for simplicity with clean lines and pretty easy designs that help artwork look sharp and friendly in the end product.
Use Bold Fonts
Always ensure that the text in your design is clear and easy to read, regardless of the fabric or material it will be printed on. Use legible fonts with adequate spacing, and avoid overly intricate or decorative typefaces that may lose clarity. Proper contrast between text and background colors is essential to maintain visibility and impact.
Experiment with Colors
Experiment with different color combinations to find your designs' most vibrant and visually appealing results. Testing various palettes ensures your final print stands out and complements the fabric or material effectively.
Mockup Your Designs
Always preview your digital mockup designs to visualize their appearance on the final product. If construction, color, or proportion issues are found, they can be located easily before printing, saving time and material.
Common Challenges in DTF Printing
DTF printing is a perfect way to print anything. However, users need to solve certain issues to get the best results. For example, it requires a proper application of adhesive powder and a consistent heat setting for the ink to adhere to the transfer film. For color reproduction, the print heads get clogged, which is due to the use of specialized DTF inks with durability on different fabrics.
1. Color Accuracy Issues
2. Uneven Adhesive Application
3. Design Smudging
Color Accuracy Issues
Calibrate your monitor and printer: Calibration allows both monitor and printer to provide the same color on both ends. It bridges digital design and print output, minimizing color discrepancies and allowing for more precise results.
Uneven Adhesive Application
The solution is to use tools like a shaker to apply adhesive powder consistently and even across the transfer film. This ensures proper design adhesion to the fabric and prevents uneven prints or durability issues.
Design Smudging
The solution is to handle the film carefully after printing to prevent smudging or damage to the design. Use clean, dry hands or gloves to maintain the integrity of the print and ensure flawless results during the transfer process.
Conclusion
It's appealing to have your own DTF designs; it lets you customize them and unleash creativity that goes beyond the limits. You can learn how to do DTF printing by following the steps in this guide. So, for any professional printing needs or help, you can trust Cheetah DTF, the track-setting leader in DTF printing services. Their delivery and dedication to quality make them a one-stop destination for DTF. So why wait; start your journey toward DTF design, and let your creativity soar!