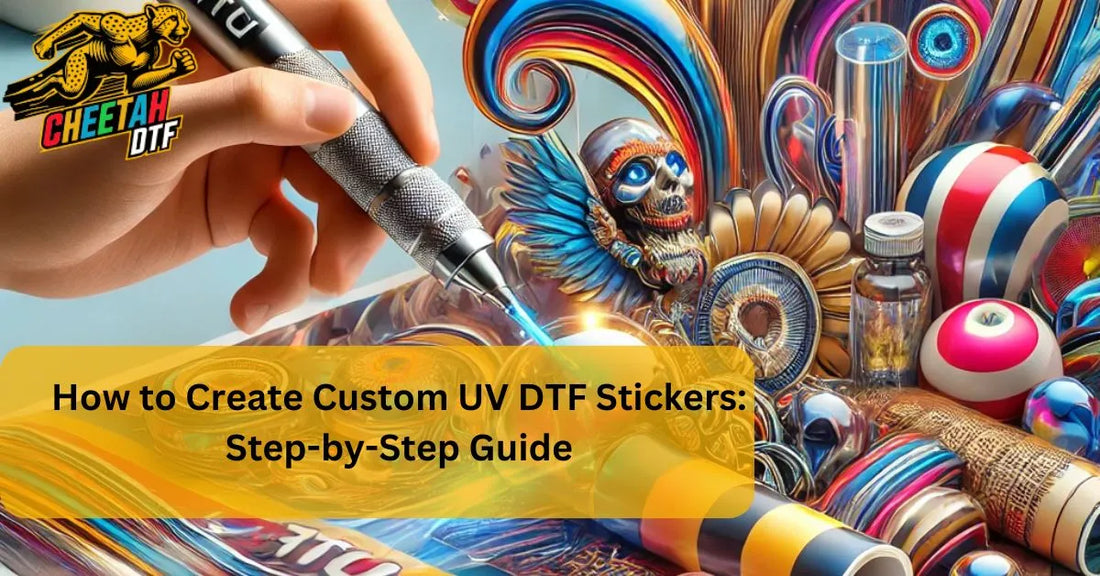
How to Create Custom UV DTF Stickers: Step-by-Step Guide
Share
Making your own UV DTF stickers is a cool and modern way of branding products, personalizing objects, and achieving highly durable prints of superior quality. This guide features a detailed step-by-step procedure to help you accomplish this task efficiently and successfully. Whether you are a beginner in UV DTF printing or an experienced professional seeking best practices, this intensive guide will help you get perfect results every time.
What is UV DTF?
UV DTF, or ultraviolet direct-to-film, is a unique printing operation that transfers designs onto multiple substrates, including glass, plastics, metals, and wood. Compared to traditional DTF, UV DTF inks are cured under UV radiation and instantaneously dried, making them far more durable, scratch-resistant, and bright--with traditional DTF, inks are just dried.
Key Features of UV DTF Stickers
UV DTF (direct-to-film) stickers are generally durable, bright, and versatile across all mediums. They present in high definition and are glossy, waterproof, scratch-resistant, and UV-resistant, thus ensuring long-lasting use indoors and outdoors. Unlike regular stickers or decals, these UV DTF stickers do not require a heat press but bond quickly to glass, plastics, metals, and wood using a high-tack adhesive. Their flexibility and easy application allow branding, promotional material, or decorative purposes to be customised.
- High durability
- Versatility
- There is no need for heat-pressing
- Professional finish
High durability
These stickers are water-resistant, thereby maintaining their durability when wet by not peeling or fading. They retain color vibrancy under harsh UV rays, making them perfect for outdoor use. Heat, dust, moisture, etc., do not affect the durability of these stickers- it gives them a tough life!
Versatility
These stickers adhere easily with a strong bond and won’t peel off on irregular, curved, and textured surfaces. Their flexibility also makes them easy to apply to products such as bottles, helmets, and curved signs.
No need for heat-pressing
UV DTF stickers stick directly under ambient conditions without the aid of a heat press, making application fast and easy. No heat is involved, eliminating the risk of heat damage and ensuring that they can be used seamlessly on heat-sensitive surfaces.
Professional finish
The UV DTF stickers boast a high resolution and are eye-appealing due to pronounced colors and a glossy finish.
UV DTF is widely used in custom branding, product sticker labels, promotional stickers, and personalized designs. This technology is incredibly popular for businesses looking for the highest-quality and most durable designs for their product packaging.
How is UV DTF Different from Regular DTF?
UV DTF (direct-to-film) differs from standard DTF in the printing technology utilized and the subsequent curing process. DTF works by heat-transferring prints onto fabric. However, UV DTF employs ultraviolet light to cure ink onto the film without heat transfer directly. Since the UV process makes the designs resistant to fading, water, and UV rays, it enhances color brilliance and durability. UV DTF has an even broader range of applications than traditional DTF, and it can be used on materials and surfaces that are sensitive to heat, while traditional DTF works mainly on fabrics. The advancement of the process yields a more accurate and finer finish than conventional DTF transfers.
1. Ink Type
2. Application Process
3. Durability
4. Surface Compatibility
Ink Type
UV DTF operates with UV-curable inks that are immediately subjected to UV light curing for very fast drying and durable results. Normal DTF uses water-based or pigment inks that transfer through heat to make a permanent bond with the surface. This makes UV DTF more efficient and versatile for heat-sensitive materials. In contrast, regular DTF takes longer and requires special equipment for transfers.
Application Process
The UV DTF stickers are transferred directly onto the surface without heat pressing, speeding up and giving versatility to the process. In contrast, the ordinary DTF requires a heat press to transfer the design onto fabrics or other materials. This adds extra time and steps to the process, making UV DTF much more handy for delicate items that are sensitive to heat or cannot withstand high temperatures. Regular DTF may have a deadly effect, but its limitation comes from applying heat.
Durability
It is waterproof and wear-and-tear resistant, making it perfect for a long-lasting finish even in tough conditions. In general, DTF supplemented with a UV stabilizer has more fade resistance from UV exposure, particularly for outdoor applications. This makes UV DTF the best for both indoor and outdoor applications. On the other hand, regular DTF is good, but maintaining vibrancy over time requires extra care.
Surface Compatibility
With its vast application versatility, UV DTF can be utilized on practically any surface-glass, plastics, metals, wood, and ceramics. In contrast, normal DTF is mainly meant for textiles: t-shirts, hoodies, and other fabric-based materials. Thus, UV DTF can be used on more materials, while DTF is used more for specialized fabrics. UV DTF permits a broader range of design options outside textile work.
These differences make UV DTF a better option for businesses that require long-lasting, professional-quality stickers that do not require heat press application.
Prep Your Surface and Pre-Squeegee Your UV-DTF PermaSticker
For proper sticker installation, highly emphasize the cleaning of surfaces to remove dust, dirt, or oils. Surfaces should be cleaned sufficiently smooth and clear of dust by applying an appropriate cleaning solution, preferably with a soft or microfiber cloth. After washing, the sticker, in general, must be positioned pre-squeegeeing with any flat object or squeegee tool and carefully rubbed down with the object from the centre onto the surface toward the outside. This permits a stronger adhesion bond and keeps the air bubbles out, allowing for a better application and a more professional finish.
- Clean the Surface
- Pre-Squeegee the UV-DTF Sticker
Clean the Surface
To maintain the integrity of the surface, dirt, grease, or debris should first be cleaned with isopropyl alcohol or a light detergent with water. Scrubbing will leave scratches on the surface; instead, wipe gently with a clean rag or a microfiber towel, wiping all areas where the sticker will be placed.
Pre-Squeegee the UV-DTF Sticker
This latter helps bond the ink and the adhesive, thereby preserving the design. Applying even pressure enables better transfer capability while minimizing the chances of air bubbles or misalignment. For best results, always work from the center outward. This will guarantee that your sticker has the best likelihood of adhesion and finish possible.
Separating The Clear Carrier Sheet From The White Backing
Begin by slightly raising a corner of the sticker to remove the transparent carrier sheet from the white backing. Remove the sheet slowly at a constant angle while ensuring that the printed design stays on it. If any portions of the design remain on the white backing, press down firmly and try again. Be careful; this can stretch or misalign the design, preventing a smooth transfer onto the desired surface.
How to Separate Them
- Gently lift a corner of the transparent carrier sheet.
- Peel back slowly and evenly to avoid damaging the design.
- If the design does not stick to the clear carrier, use the squeegee again to reinforce adhesion.
This step ensures the sticker is lifted correctly and ready for placement.
Placing Your UV-DTF PermaSticker Onto Your Item
To apply your UV-DTF PermaSticker, first ensure the surface is clean, dry, and free of dust or oil to optimise adhesion. Peel off the backing carefully, align the sticker on your item, and press down firmly from the center to the outer edge to push out any air bubbles underneath. Allow proper setting to create a strong bond on flat, curved, or textured surfaces for a long-lasting effect.
Proper Placement Techniques
When applying UV-DTF stickers, achieving the best adhesion characteristics starts with a smooth, clean, and dry surface. Use a measuring device or guide to position the sticker and prevent accidental misplacement. When applying, start from the center and work outward to expel air bubbles under the sticker and ensure even contact. Apply light pressure along the edges while smoothing out the design to avoid any lifting around the edges for curved surfaces or textured surfaces. Taking time to place artwork properly will improve durability and the look.
- Align the sticker on your item, ensuring it is straight and centred.
- Slowly press it onto the surface, starting from one side to avoid air bubbles.
- Use a squeegee or soft cloth to press down firmly, ensuring proper adhesion.
Apply the sticker gradually while pressing down for curved surfaces to maintain a smooth finish.
Completing the Transfer Process
The remaining steps are to carefully and slowly peel off the transparent carrier sheet from the sticker at an angle so that the design remains adhered to the surface. If the sticker starts to lift at any point, you will want to press it back with a squeegee or even your fingers, and you can apply even pressure to ensure bonding. Next, check the edges and corners after removing the carrier sheet to confirm everything is bonded completely. Also, set that sticker for a couple of hours to ensure you would have it bonded very well. This last step provides your design with a smooth finish that is well adhered to and ready for action.
Final Transfer Steps
Carefully peel the transparent carrier sheet back, ensuring the design adheres to the surface. If any part does not stick completely, press it down again. Please inspect for bubbles and lifting edges and use a squeegee to smooth them down for a perfect finish. Once the transfer is complete, let the design set for 24 hours for extra adhesion and durability.
Conclusion
Be it custom branding stickers, promotional decals, or product labels, Cheetah DTF always delivers mind-blowing quality. Get premium UV DTF stickers from Cheetah DTF today to give your products that extra kick!
Go step by step in this guide to produce professional-grade UV DTF stickers that work towards branding, boost customer engagement, and add a personal touch to any product. Cheetah DTF knows custom printing; therefore, you will be assured of getting some of the finest UV DTF stickers available. Cheetah DTF is a name the industry trusts regarding high-quality UV DTF sticker printing. Their expertise in custom DTF printing services ensures you get durable, vibrant, and precision-cut stickers tailored to your needs.
FAQs
What is the difference between UV DTF and regular DTF printing?
The inks used in UV DTF are instantaneously cured under UV light and offer enhanced durability. They are also highly versatile and brightly coloured. At the same time, the regular DTF applies heat transfer designs to the fabric, which works only on select surfaces and affects its durability.
Can UV DTF stickers be applied to any surface?
Indeed, UV DTF stickers are very versatile, as they can be applied to a wide range of surfaces, including glass, plastic, metal, wood, and ceramics. DTF, however, is primarily intended for use in textiles.
How do I ensure the UV DTF sticker adheres properly to my item?
Clean the surface thoroughly to eliminate dust or grease. Using a squeegee, gently remove the sticker from the center to the outside to push out any air bubbles and ensure it sticks perfectly.
How long should I wait before using my UV DTF sticker after application?
After attaching the decal, let it stay for 24 hours so that it may get efficiently stuck and be within reach. This will ensure such potential good work and total adhesion finish, too.