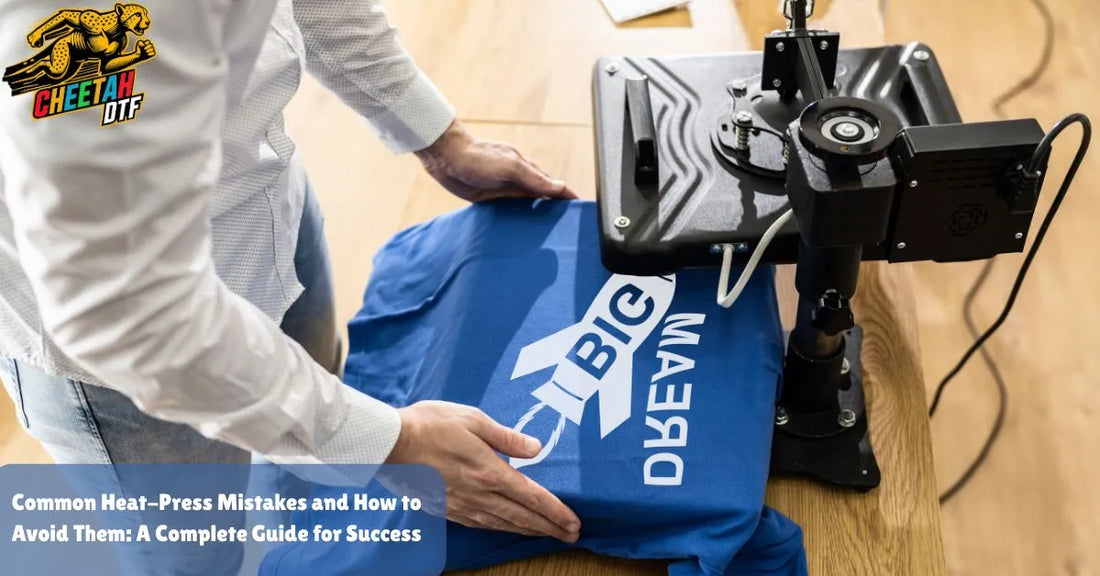
Common Heat-Press Mistakes and How to Avoid Them: A Complete Guide for Success
Share
Learn about the most common heat-press mistakes and how to fix them. From HTV not sticking to sublimation ghosting, get tips for perfect heat transfer.
Heat pressing is a crucial technique in the world of custom apparel and printing, but even the most experienced users can mess up. From wrong temperatures to misaligned designs, these mistakes can ruin your heat-press projects. In this article, we’ll go over common heat-press mistakes and give you actionable tips on how to avoid them. Whether you’re dealing with HTV not sticking after pressing, sublimation ghosting or uneven heat press pressure, we’ve got you covered.
Heat-Press Mistakes: The Most Common Errors
One of the biggest mistakes when working with a heat press is not preparing your machine. Having the wrong temperature, time, and pressure will give you poor-quality transfers. Beginners also don’t pre-press the fabric, which leaves the vinyl wrinkled and with low adhesion. You need to know your heat press settings and how to adjust them based on the material you’re using.
Before you start your next heat press project, make sure your press is clean, the temperature is calibrated, and the pressure is set to the right level for the material you’re working with.
HTV Not Sticking After Pressing: What Went Wrong?
One of the biggest issues with heat transfer vinyl (HTV) is when it doesn’t stick after being pressed. There are several reasons why. The biggest reason is not having the right temperature or pressure. HTV should be applied at high temperatures to stick properly on fabrics, usually between 300°F and 320°F, depending on the brand.
Another reason HTV might not stick is when the fabric is too textured or not ready. Make sure to pre-press the fabric to remove any moisture and get rid of wrinkles before adding the HTV. If you’re working with a polyester fabric, the vinyl might not stick well since the surface is too smooth.
How to Fix Heat Transfer Peeling
Peeling caused by heat transfer is a common issue that happens when the design is peeling or coming off the fabric after being pressed. It’s usually caused by too low heat or pressure when being pressed. To fix peeling caused by heat transfer, make sure the heat press is at the right temperature and pressure. If the temperature and pressure is correct and the peeling is still being seen, try to press the item a few seconds longer or with a bit more pressure.
Also, make sure you’re peeling off the backing at the right time. Peeling off too quickly will mean peeling, and peeling off too slowly will mean the design will stick to the carrier sheet.
Sublimation Ghosting Issues: How to Prevent Them
Sublimation ghosting happens when the sublimation ink is applied slightly off-center, creating a doubled or fuzzy picture. It can be caused by substrate shifting when you apply pressure or by inconsistent temperature. Sublimation ghosting should be avoided by keeping your substrate firmly in place using thermal adhesive spray or heat-resistant tape.
Another preventive measure is to keep the right temperature, which is usually 400°F when it comes to sublimation. Sublimation ghosting also happens when the substrate is not preheated, meaning it’s not evenly heated. Always pre-press your fabric to get an even temperature before you sublimate.
Heat Press Pressure Problems: Fixing Uneven Pressure
Heat press pressure problems are another common issue when it comes to heat pressing. When the pressure is not uniform, certain areas of the design won’t transfer well, leaving patchy or incomplete designs. This is when the pressure is too light or not uniform across the press.
To maintain even pressure when using a heat press, make sure the heat press is calibrated. Vary the pressure depending on the material you’re working with. Polyester and cotton fabrics may require different pressures. Also, make sure the platen on the heat press is level and not blocked by any obstruction that might hinder even pressure distribution.
Scorch Marks on Heat-Press Designs: How to Avoid Damage
Scorch marks on designs on a heat press mean overheating or too much time on the press. Excessive temperature or too much time on the design with the press will burn the fabric or leave ugly marks. Scorch marks usually happen on fabrics like HTV and sublimation when the press is not monitored closely. How to avoid scorch marks is by always using the right temperature for the material. For most fabrics, 250°F to 300°F is ideal. For HTV, 300°F to 320°F is the ideal temperature. Also, don’t leave the heat press on the fabric for too long; check the recommended time and stick to it.
Why Does Vinyl Wrinkle After Pressing?
Wrinkling After Pressing is a frustrating issue, yet it’s usually preventable. The biggest reason it happens is either the temperature is too high or too low or the pressure is too light. When using HTV, It’s important to press at the correct temperature and pressure depending on the brand of vinyl.
Vinyl will wrinkle when the fabric is not pre-pressed because moisture or wrinkles will hinder the smooth transfer of the vinyl. Always pre-press the fabric for 5-10 seconds to drive out moisture and wrinkles before you apply the vinyl.
Overheating HTV: What You Need to Know
Overheating HTV is a common problem when you set the temperature of the heat press too high compared to the type of vinyl you’re using. This will cause the vinyl to shrink, change color or even melt in the process. Overheating HTC also results in improperly applied designs which then peel and lift.
Overheating of HTV is avoided by always following the manufacturer’s temperature guidelines. Most HTV is pressed between 300°F and 320°F, but it’s always good to check the instructions on the vinyl so you know the correct settings. Keeping the correct pressure and time will also prevent overheating.
Fading Sublimation Prints: Causes and Solutions
Sublimation prints fade when the dye doesn’t bond properly with the fabric and the prints lose color over time. The major cause is low temperature when it comes to the press phase. When the temperature is low, the sublimation ink will not bond properly with the fiber of the fabric, and the design will fade.
Preventing Sublimation Print Fading
Make sure your heat press is at the right temperature (around 400°F) and press it for the required time. Also, use good quality inks and sublimation paper as low quality materials will cause fading.
Fixing Uneven Heat Press Pressure: A Step-by-Step Guide
Uneven heat press pressure is a common cause of poor transfers with partial or incomplete designs. To fix uneven heat press pressure first make sure your heat press is calibrated. The pressure should be even across the entire platen so the heat and pressure apply evenly.
Start by adjusting the pressure knob or dial on your heat press to the right level depending on the fabric you will be pressing. For heavy fabrics, you may have to set it higher, like in the case of sweatshirts, and thinner fabrics like cotton t-shirts may require less pressure.
Conclusion
Heat pressing is a fun process when done right, but it’s easy to get it wrong. Knowing the common heat press mistakes and how to avoid them will save you time, money and hassle in the long run. From HTV not staying on after being pressed to ghosting when doing sublimation, every single one of the mistakes has a solution, and with the tips above, you’ll be producing perfect prints every time.
Make sure your heat press is set right, you’re using good quality materials, and you’re paying attention to the details of the correct temperature, pressure and time so your designs always come out perfect.